Cold Storage Warehouse
​When tasked with inspecting the roof of a cold storage warehouse in western Washington, my team encountered unique challenges. The manager expressed concerns about ice buildup in the roofing system, and the company was considering a full roof tear-off and replacement.
​
The most significant challenge was the ballasted roof, which consisted of a 2-inch layer of gravel atop the roofing membrane. This gravel layer—over 40,000 cubic feet or more than 1,150 cubic yards—complicated inspection efforts. The size of the gravel itself posed thermal challenges, as smaller rock retains heat longer due to the insulation beneath the membrane.
​
To overcome these obstacles, we utilized advanced drone-mounted thermal imaging technology. Conducting multiple flights throughout the night, we gathered detailed thermal images of the roof.
Our results provided critical insights, allowing the manager to validate the recommendation of one roofing contractor over others. This decision ultimately saved the company an estimated $400,000, according to the manager.
Cold Storage Roof Inspection: Saving Time and Costs with Thermal Imaging
​
​
Why Choose Drone Thermal Imaging for Roof Inspections?
-
Cost Savings: Accurate thermal imaging prevents unnecessary expenses by pinpointing exact problem areas.
-
Time Efficiency: Drone inspections take hours, not days, even for large, complex roofs.
-
Detailed Results: High-resolution thermal images provide actionable insights for informed decision-making.
For complex roofing systems like cold storage warehouses with ballasted roofs, thermal imaging is a game-changing solution that saves time, money, and resources.

.png)
.png)
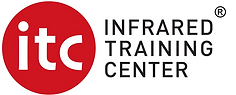